ADVANCED NON-DESTRUCTIVE TESTING.
Non-Destructive Testing has radically changed emphasis over recent years from a focus on detecting defects arising during the manufacture of new products, to detecting process induced integrity problems. ODAK NDT TECHNOLOGIES PVT LTD has established itself at the forefront of an NDT technological revolution by a process of investment in state-of-the-art equipment and specialized training to meet this step-change. The result is an infrastructure that offers a comprehensive range of Advanced NDT (ANDT) that individually or in combination provide state of the art solutions to the ever-increasing demand for Non-Invasive Inspection.
From strategically located centres of excellence, our services are coordinated on a worldwide basis and offer a proven record of delivering a safe, technically sound and cost effective service. The Qualitas Inspection department employees experienced fully qualified NDT level III technical support personnel who maintain the organizations competitive advantage by constantly monitoring and evaluating incremental and radical innovations in inspection technology.
Advanced NDT Services We Provide:
PHASED ARRAY ULTRASONIC TESTING (PAUT)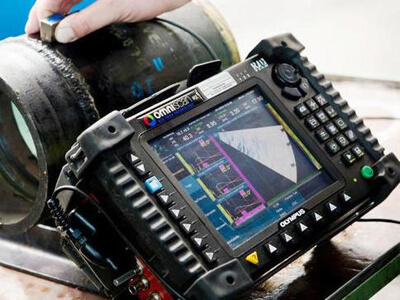
Phased array (PA) is widely used in several sectors, from power generation to construction industries. It is an advanced non-destructive testing (NDT) method that uses an ultrasonic technique to determine component quality and detect failure such as flaws or cracks. Furthermore, Phased Array Ultrasonic Testing can be effectively used for wall thickness measurements in conjunction with corrosion testing. Its efficiency comes from the combination of many angles and focus depths through to one probe which then performs several different inspections without the need for changing the transducer assembly. The inspection results are clearly stored and displayed for reporting. It can be used on standard and special materials like austenitic and high alloy materials.
Qualitas NDT Inspection Services is specialized in providing a complete range of advanced non-destructive testing (NDT) services. In addition to operating a competence center for advanced NDT based in the UAE, and we invests heavily in R&D and operates an accredited training school for advanced NDT as well as offering its expert services globally.
ADVANTAGES:
- Simplified inspection of components that have complex geometry.
- Inspection of many different materials possible.
- High temperature inspections possible up to over 350 C.
- Speedy inspection compared to conventional ultrasonic testing.
- Higher probability of problem detection thanks to testing from multiple angles with a single probe.
- All inspection data presented in an understandable graphic format.
- Well qualified operators.
TIME OF FLIGHT DIFFRACTION (TOFD)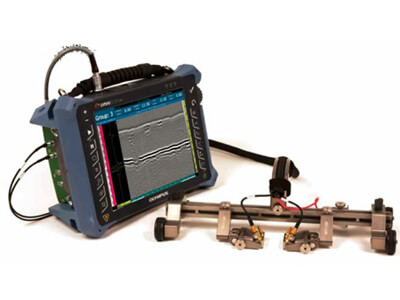
Welding defects can compromise the stability and integrity of a welded structure. When you need confidence in testing of welds, Time of Flight Diffraction (TOFD), a high performance non-destructive testing (NDT) technique offers you accurate detection of cracks, slag and lack of fusion.
We accompany you throughout your testing project and offer you individual solutions. Our capabilities include weld testing using TOFD technique, data processing and report preparation using the developed software. We believe that using our TOFD inspection service will lead to major time savings during the life cycle of new build and replacement projects. It is an excellent and widely accepted pre-service and in-service inspection tool that is recognized internationally, with defined codes, standards and acceptance criteria available for its use.
ADVANTAGES:
- Higher probability of failure detection compared to conventional procedures such as radiographic testing (RT) and ultrasonic testing (UT).
- Reduced costs, as TOFD inspections can take place on-site alongside production work during the day shift.
- No logistical difficulty as in the case of radiographic testing.
- Quick results, as inspection time is not as highly affected by material thickness as it is in the case of radiographic testing.
- Material examinations and inspections are possible even to temperatures exceeding 400 C.
- Reduced risk of company liability thanks to documented safety standards.
- Well qualified operators.
- Certified inspectors in accordance with the TOFD certification program based on ISO 9712 (former EN 473).
REMOTE VISUAL INSPECTION/VIDEOSCOPY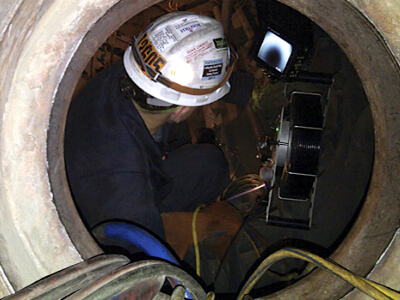
Remote Visual Inspection or Remote Digital Video Inspection, also known as RVI or RDVI, is a form of visual inspection which uses visual aids including video technology to allow an inspector to look at objects and materials from a distance because the objects are inaccessible or are in dangerous environments. RVI is also a speciality branch of non-destructive testing (NDT).
Technologies include but not limited to rigid or flexible borescopes, videoscopes, fiberoscopes, push cameras, pan/tilt/zoom cameras and robotic crawlers. Remote are commonly used where distance, angle of view and limited lighting may impair direct visual examination or where access is limited by time, financial constraints or atmospheric hazards. RVI/RDVI is commonly used as a predictive maintenance or regularly scheduled maintenance tool to assess the “health” and operability of fixed and portable assets. RVI/RDVI enables greater inspection coverage, inspection repeatability and data comparison. The “remote” portion of RVI/RDVI refers to the characterization of the operator not entering the inspection area due to physical size constraints or potential safety issues related to the inspection environment.
APPLICATIONS:
- Aircraft engines (turbofan, turbojet, turboshaft).
- Aircraft fuselage.
- Turbines for power generation (steam and gas).
- Process piping (oil and gas, pharmaceutical, food preparation).
- Nuclear Power Stations – contaminated areas.
- Any areas where it is to dangerous, small or costly to view directly.
ADVANTAGES:
- Less mechanical disassembly to access subject areas.
- Reduced NDT costs over other forms of testing.
- Reduced shut down times and faster reinstatement of equipment.
- Fewer safety constraints over manual inspection methods.
- Faster, accurate monitoring of equipment condition during life cycles.
- Better assessment of condition and timing prior to critical maintenance.
- Faster identification, location and isolation of faults.
LONG RANGE UT(LRUT)
Long range ultrasonic testing is a rapid way of screening for corrosion in pipelines. The method enables screening of up to 100 meters of pipeline in one test, i.e. 50 meters in both directions.
By fitting a ring of transducers around the pipeline, a wave maker device directs low frequency (20-100 kHz) ultrasonic waves via the transducers, longitudinally into the pipeline wall. The method effectively detects changes in the pipeline cross-section, enabling it to identify corrosion and other abnormalities. At the same time this provides the possibility of using welds and flanges as distance references.
ALCO INSPECTIONS has qualified experts in using this method to help you get a cost-effective report on the condition of your pipelines.
ADVANTAGES:
- More than 100 times faster than traditional ultrasonic methods.
- Up to 100 meters screening distance on pipelines above ground.
- Up to 10 meters screening distance on pipelines buried in the ground.
- Possibility to do sub-sea scanning.
- Saves time since there is no need to remove insulation, apart from 1 meter for the transducer ring.
- Easy to screen wall penetrating pipelines (both built-in and sleeved penetrations).
MAGNETIC FLUX LEAKAGE(MFL- 3D VERSION)
Magnetic flux leakage (MFL) is a magnetic method of non-destructive testing that is used to detect corrosion, pitting and wall loss in steel structures.
Magnetic flux leakage (MFL) is commonly used for inspecting tank floors in the petrochemical industry. Corrosion of the tank floor can lead to the loss of product and cause damage to the environment. Therefore, it is vital that tank floor inspections are carried out in order to prevent the occurrence of such problems.
MFL provides a cost-effective and high-speed inspection of tank floors. Our qualified MFL inspectors are backed by years of experience. We use MFL equipment such as Floormap VS2i and Floormap 3D.
The method uses permanent or electromagnets to magnetise the tank floor and the resulting magnetic field changes are recorded and analysed. If there is corrosion, pitting or wall loss, the magnetic field leaks and the leakage is analysed to determine the location and severity of the defect of the tank floor both near and far surface. A map of the corroded areas is provided with the MFL method and this essential data can be stored for future reference and planning.
ADVANTAGES:
- Determining Corrosion Growth Accurately and Reliably.
- Magnetic flux leakage as applied to aboveground storage tank flat bottom tank floor inspection.
REMOTE FIELD ELECTROMAGNETIC TESTING (RFET)
Remote Field Testing or “RFET” is one of several electromagnetic testing methods commonly employed in the field of non-destructive testing. Other electromagnetic inspection methods include magnetic flux leakage, conventional eddy current and alternating current field measurement testing. Remote field testing is associated with eddy current testing and the term “Remote Field Electromagnetic Testing” is often used when describing remote field testing. However, there are several major differences between eddy current testing and remote field testing which will be noted in this section.
RFET is primarily used to inspect ferromagnetic tubing since conventional eddy current techniques have difficulty inspecting the full thickness of the tube wall due to the strong skin effect in ferromagnetic materials.
For example, using conventional eddy current bobbin probes to inspect a steel pipe 10 mm thick (such as what might be found in heat exchangers) would require frequencies around 30 Hz to achieve the adequate I.D. to O.D. penetration through the tube wall. The use of such a low frequency results in a very low sensitivity of flaw detection. The degree of penetration can, in principle, be increased by the use of partial saturation eddy current probes, magnetically biased probes, and pulsed saturation probes. However, because of the large volume of metal present as well as potential permeability variations within the product, these specialized eddy current probes are still limited in their inspection capabilities.
The difficulties encountered in the testing of ferromagnetic tubes can be greatly alleviated with the use of the remote field testing method. The RFET method has the advantage of allowing nearly equal sensitivities of detection at both the inner and outer surfaces of a ferromagnetic tube. The method is highly sensitive to variations in wall thickness and tends to be less sensitive to fill-factor changes between the coil and tube. RFET can be used to inspect any conducting tubular product, but it is generally considered to be less sensitive than conventional eddy current techniques when inspecting non-ferromagnetic materials.
ADVANTAGES:
- Suitable for ferromagnetic tubes such as those found in heat exchangers and boilers.
- Localized corrosion, Pittings.
- Equally sensitive to internal and external flaws.
- Can inspect tubes up to 75mm OD with 5mm thickness.
- Relatively insensitive to probe liftoff or wobble.
- Typical pull speed between 6 and 12 per second.
INTERNAL ROTARY INSPECTION SYSTEM (IRIS)
IRIS is an ultrasonic method used for the non-destructive testing of pipes and tubes. Many plant operators in the oil & gas and power generation industries are faced with the challenges of maximising the efficiency and life expectancy of their assets but without sacrificing safety and reliability. Therefore accurate inspection of vital components such as pipes and tubes is crucial to ensuring the integrity of the plant.
Internal Rotary Inspection System (IRIS) can detect corrosion, pitting and wall loss and is most commonly used for tube inspection in boilers, heat exchangers, air coolers and feed water heaters. It is particularly versatile as it is suitable for both ferrous and non-ferrous materials, and IRIS can be used on a wide range of tube diameters and wall thickness.
An IRIS probe is inserted into a tube flooded with water. The probe is fitted with a transducer that generates an ultrasonic pulse along a path parallel to the axis of the tube. A rotating mirror directs the ultrasonic pulse into the tube wall. The mirror is driven by a small turbine that is rotated by the pressure of water pumped into the tube.
The ultrasound pulses are reflected by the inner-diameter (ID) wall and outer-diameter (OD) wall of the tube and the time of flight difference between the two diameters is used to calculate the wall thickness. As the IRIS probe is pulled, the spinning motion of the mirror results in a helical scan path ensuring full coverage of the tube.
ADVANTAGES:
- Suitability for ferrous and non-ferrous materials.
- Detection of corrosion, pitting and wall loss.
- Accurate wall thickness measurements.
- Sensitivity to both internal and external defects.
- Defect position can be located in relation to tube length.
- Flexibility as a back-up to remote field, magnetic flux leakage and eddy current inspections.
Near Field Testing (NFT)
NFT is a technology that uses two coils a transmitter and a receiver. Typically the receiver coil is close to the transmitter coil, taking advantage of the transmitter near-field zone that is, the zone where the magnetic field from the transmitter coil induces strong eddy currents, axially and radially, in the tube wall.
NFT probes operate within the same frequency range as remote-field testing (RFT) probes.
NFT is specifically suited to detecting corrosion, erosion, and pitting inside carbon steel tubing. NFT is perfect for fin-fan tube heat exchanges because eddy currents do not go through the wall of the tube. NFT is also much more sensitive to defects close to structures such as support plates and tube sheets
ADVANTAGES:
- Fast Inspection.
- No need for an external reference coil.
- Easy to use.
- Unaffected by structures such as support plates and tube sheets.
ACOUSTIC EMISSION (AE)
Acoustic emission testing is a non-destructive testing method designed to monitor sound waves emitted during material stress or failure. This condition monitoring method enables inspectors to examine metal deformation under stress and detect the sound of cracks and failures growing within the material. If you need to detect flaws in metallic pressure equipment , acoustic emission testing is one of the most reliable ways to detect the early stages of stress corrosion cracking. When a material undergoes stress or a series of internal changes such as corrosion, it generates energy from localized sources which produces sound waves.
Unlike other non-destructive testing methods, AE testing does not send energy into the inspected pressure vessel, but rather detects the energy emitted by the equipment itself. This technique is therefore time-effective because it can be performed during material operation. Acoustic emission testing enables you to monitor and inspect your entire pressure equipment, from tanks to welds. It provides immediate results and early warning of possible damage or failure in pressure equipment as well as solutions to determine the appropriate pressure level.
ADVANTAGES:
- Early detection of flaws and corrosion cracking.
- Inspection and testing of your equipment while in operation.
- Significant cost savings for vessels with complex geometries.
- Integral non-destructive testing and monitoring of your pressure equipment.
ALTERNATING CURRENT FIELD MEASUREMENT(ACFM)
Alternating current field measurement (ACFM) is an electromagnetic technique used for the detection and sizing of surface breaking cracks in metallic components and welds. It combines the advantages of the alternating current potential drop (ACPD) technique and Eddy Current Testing (ECT) in terms of defect sizing without calibration and ability to work without electrical contact respectively.
The ACFM probe introduces an electric current locally into the part and measures the associated electromagnetic fields close to the surface. The presence of a defect disturbs the associated fields and the information is graphically presented to the system operator. The ends of a defect are easily identified to provide information on defect location and length. Through wall extent of the flaw plays an important role in determining structural integrity and the same is calculated using mathematical computation thus allowing an immediate evaluation of the implication of the indication. ACFM inspection can be performed through paint and coatings, hence it is considered to be a faster and economic technique than others (E.g. magnetic particle inspection (MPI).
ADVANTAGES:
- Applicable for base material or welds, ferritic or non-ferritic conductive metals.
- Can be used on hot surfaces, underwater, or in irradiated environments.
- Provides both depth and length information.
- Accurate sizing of defects up to 25mm in depth.
- Requires minimal surface preparation and can be applied over paint and other coatings.
- Applicable for under water inspection as well as normal inspection.
- Inspection data can be stored and analysed offline.
HYDROGEN INDUCED CRACKING (HIC)
Hydrogen-induced cracking (HIC) refers to the internal cracks brought about by material trapped in budding hydrogen atoms. It involves atomic hydrogen, which is the smallest atom, that diffuses into a metallic structure. In the case of a crystal lattice becoming saturated or coming into contact with atomic hydrogen, many alloys and metals may lose their mechanical properties.
ADVANTAGES:
- Applicable for base material or welds, ferritic or non-ferritic conductive metals.
- Can be used on hot surfaces, underwater, or in irradiated environments.
- Provides both depth and length information.
- Accurate sizing of defects up to 25mm in depth.
- Requires minimal surface preparation and can be applied over paint and other coatings.
- Applicable for under water inspection as well as normal inspection.
- Inspection data can be stored and analysed offline.
ULTRASONIC LEAK DETECTION/HATCH COVER TEST
Ultrasonic Leak Test consists of a battery powered transmitter and a receiver. It is totally reliable, accurate and repeatable. There’s no need for water or for complicated operations. Ultrasonic testing slashes the time needed to test the condition of hatch covers, RoRo doors, bulkheads or windows. It ensures that hatch covers offer true cargo worthiness and prevent water ingress. Hand-held operation can be carried out by one man. It reduces costly idle time in port Easy, fast pre-load inspection.
The emitters are arranged to produce an omni-directional sound field, uniformly distributed throughout the cargo hold. The receiver part of the system displays the sound energy level that passes through gaps in the enclosed cargo hold to enable the location of leaks to be quickly and accurately identified.
ADVANTAGES:
- Vehicles – Wind Noise/Water Leaks.
- Ships – Hatch Cover Testing and General Surveying.
- Building – Envelope including Doors, Windows, and Ventilation.
- Tanks – Underground Fuel Storage Tanks.
INFRARED THERMOGRAPHY
DEFINITION OF INFRARED THERMOGRAPHY
Infrared thermography is equipment or method, which detects infrared energy emitted from object, converts it to temperature, and displays image of temperature distribution. To be accurate, the equipment and the method should be called differently, the equipment to be called as infrared thermograph and the method to be called as infrared thermography. Recently, however, more and more public literatures show tendency not to pay attention to such appellative. We call our equipment as infrared thermography considering such generalization of the terminology.
CHARACTERISTICS OF INFRARED THERMOGRAPHY EQUIPMENT:
- It captures as a temperature distribution on a surface,and it can display as a visible information.
- Temperature can be measured from a distance without contacting an object.
- Temperature can be measured in real time.
ADVANTAGES:
- It shows a visual picture so temperatures over a large area can be compared.
- It is capable of catching moving targets in real time.
- It is able to find deteriorating, i.e., higher temperature components prior to their failure.
- It can be used to measure or observe in areas inaccessible or hazardous for other methods.
- It is a non-destructive test method.
- It can be used to find defects in shafts, pipes, and other metal or plastic parts.
- It can be used to detect objects in dark areas.